TUBULAR HEATING ELEMENTS
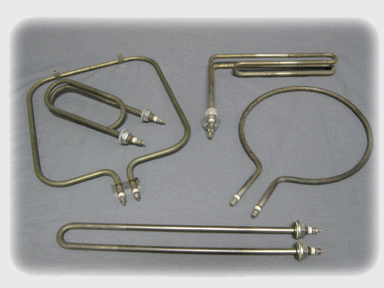
Tubular heating elements, the most versatile of all types, are used for practically the entire range of electric resistance heating applications.The metal sheath material and the proper size resistance wire for the heating element are carefully chosen and verified by computer calculations to insure the longest service life possible.
The nickel/chromium resistor wire is then fusion welded to a terminal pin to assure a positive connection. It is centered in the metal sheath and insulated with high quality magnesium oxide, (MgO). The MgO is tightly compacted around the coil and acts as an electrical insulator. The material rapidly conducts the heat from the coiled resistor to the metal sheath and puts the heat where it is required.
Nickel Chromium Resistance Wire
80% nickel, 20% chromium alloy resistance wire is the heart of the tubular element. This wire must meet strict GLO-QUARTZ® and internationally recognized standards.
MgO Insulation
Magnesium oxide insulation is carefully selected to give the best transfer of heat from resistance wire to element sheath. This allows the resistor wire to operate at the lowest possible temperature. The MgO must meet rigid GLO-QUARTZ® specifications.
Choice of Sheath Material
A selection of sheath material is available to meet an unlimited variety of applications. Standard sheath materials are Incoloy®, Types 304 and 316 stainless steel, copper and titanium.
Variety of Mounting Methods
Elements can be supplied with threaded fitting for mounting through walls of tanks, ovens, etc. Compression threaded fitting are also available for easy field installation. Rings, clips, brackets and washers can also be attached to elements for mounting purposes. See TERMINAL types.
Long Life
Tubular heaters are designed for long life and will outlast other tubular element in a given application. Proper application assures long life. Consult with one of our applications engineers for assistance.
Bending Formations
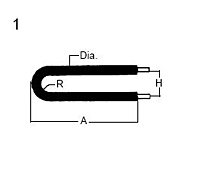
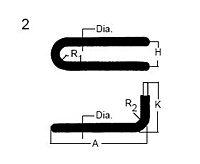
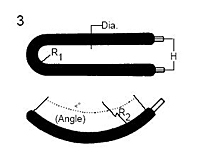
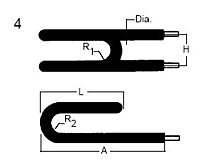
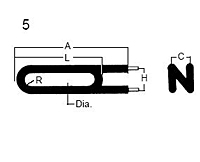
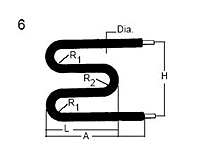
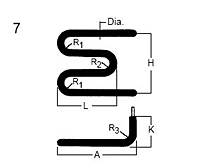
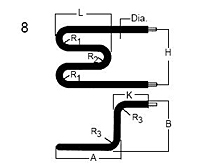
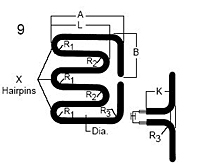
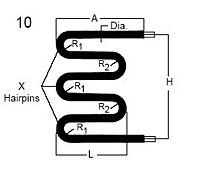
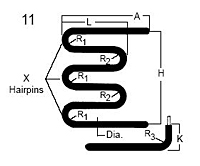
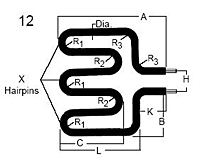
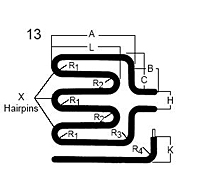
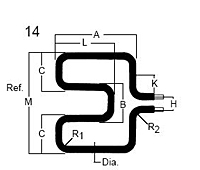
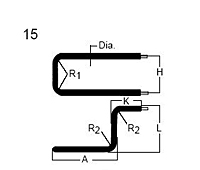
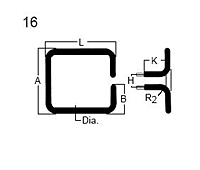
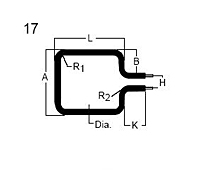
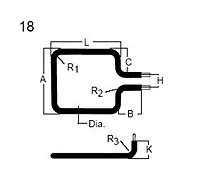
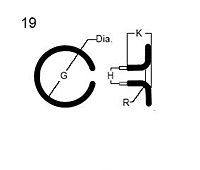
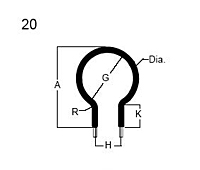
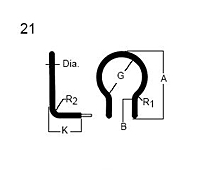
Terminal Types
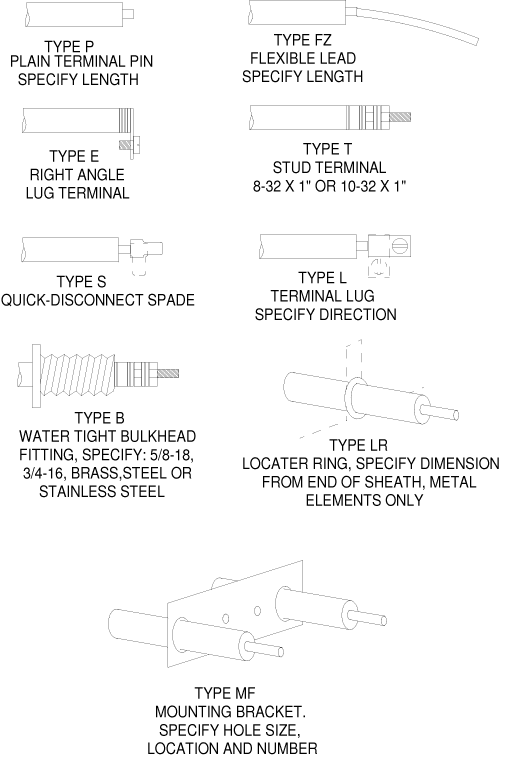